Doğru Dişli Üretim Sürecini Seçmek: Hobbing, Şekillendirme ve Taşlama
- pay
- yayıncılar
- pairgears
- Yayım tarihi
- 2024/8/8
özet
Dişlilerin üretim yöntemleri arasında çoğunlukla dişli azdırma, dişli şekillendirme ve dişli taşlama yer alır ve her birinin kendine özgü avantajları ve dezavantajları vardır.
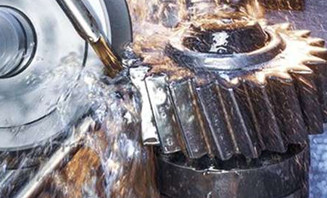
giriiş
Dişli üretimi söz konusu olduğunda, hem verimliliği hem de kaliteyi sağlamak için uygun işlemi seçmek çok önemlidir. Bu makalede, üç temel dişli üretim yöntemini inceleyeceğiz: frezeleme, şekillendirme ve taşlama ve her birinin ayrıntılı bir analizini sunacağız.
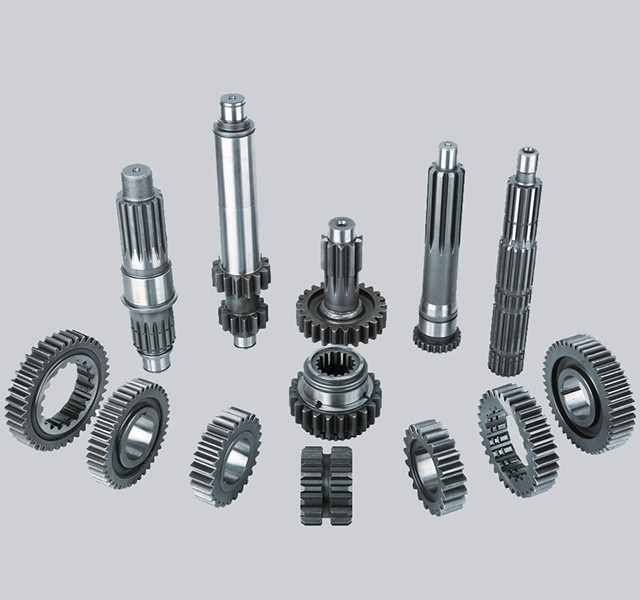
Hobbing: Hızlı ve Etkili Bir Yöntem
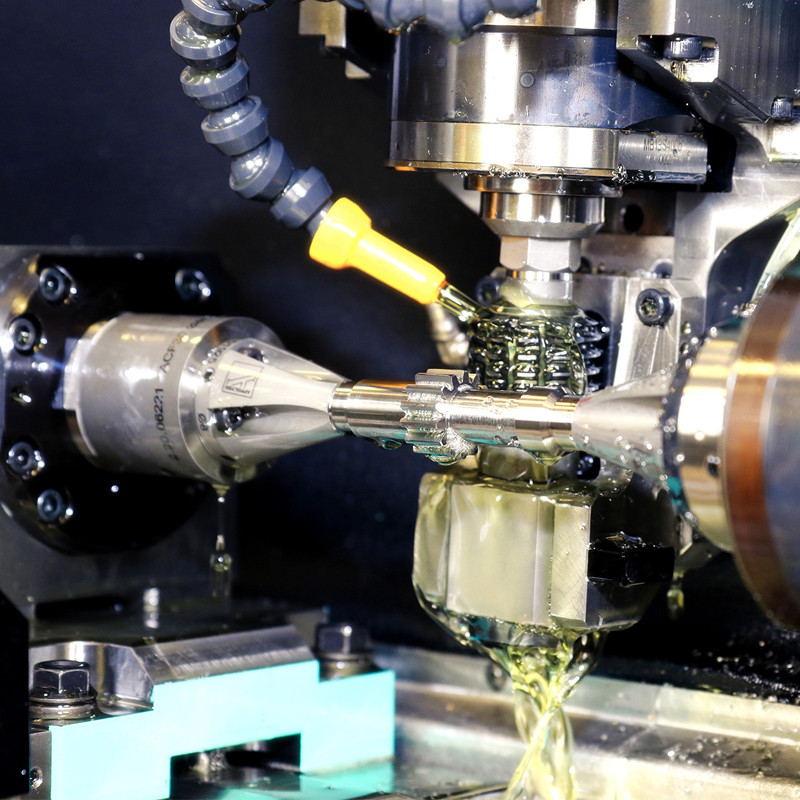
Hobbing'in Avantajları:
1. Hız: Hobbing, yüksek hacimli çalışmalar için ideal olan hızlı üretim kabiliyetiyle bilinir.
2. Çok yönlülük: Mahmuzlu, helisel ve sonsuz dişliler dahil olmak üzere çeşitli dişli tiplerinin üretiminde kullanılabilir.
3. Hassasiyet: Modern freze tezgahları, dişli diş profillerinde yüksek doğruluk seviyelerine ulaşma kapasitesine sahiptir.
Hobbing'in Dezavantajları:
1. Malzeme Sınırlamaları: Hobbing, çok sert veya kırılgan malzemeler için daha az etkili olabilir.
2. Yüzey İşlemleri: Yüzey işlemlerinin belirli standartları karşılayabilmesi için ek işlemlere ihtiyaç duyulabilir.
Şekillendirme: Geleneksel Ama Güvenilir Bir Seçenek
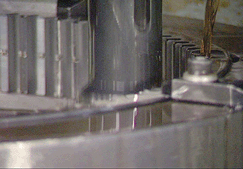
Şekillendirmenin Avantajları:
1. İyi Yüzey Sonlandırma: Şekillendirme genellikle frezelemeden daha iyi bir yüzey sonlandırma ile sonuçlanır.
2. Sert Malzemeler: Hobbing için uygun olmayabilecek daha sert malzemelerle etkili bir şekilde çalışabilir.
Şekillendirmenin Dezavantajları:
1. Hız Sınırlamaları: Şekillendirme genellikle daha yavaştır ve bu da onu yüksek hacimli üretim için daha az uygun hale getirir.
2. Takım Aşınması: Kesici takımlar, işlemin doğası gereği daha çabuk aşınabilir.
Taşlama: Hassasiyetin En İyisi
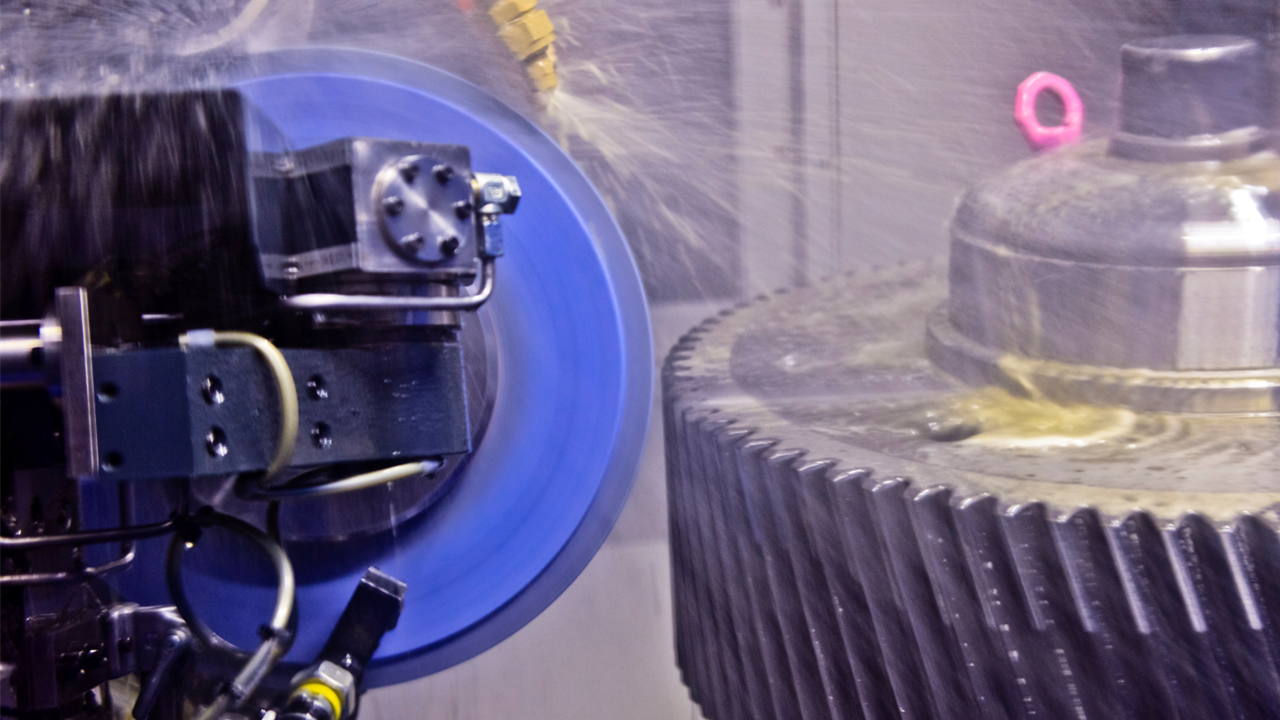
Öğütmenin Avantajları:
1. Yüksek Hassasiyet: Taşlama, olağanüstü doğruluk sunar ve sıkı toleranslar gerektiren dişliler için idealdir.
2. Mükemmel Yüzey Kaplaması: Bu işlem, dişli performansını artırabilen son derece cilalı bir yüzey elde edilmesini sağlar.
Öğütmenin Dezavantajları:
1. Yüksek maliyet: Dişli taşlama makineleri pahalıdır ve taşlama işleminin kendisi zaman alıcıdır ve malzeme tüketir, bu da daha yüksek üretim maliyetlerine yol açar.
2. Düşük verimlilik: Dişli taşlama işleminin işleme hızı daha yavaştır ve seri üretime uygun değildir.
Çözüm
Doğru dişli üretim sürecini seçmek - ister taşlama, ister şekillendirme veya taşlama olsun - üretim hacmi, malzeme türü ve hassasiyet gereksinimleri gibi çeşitli faktörlere bağlıdır. Taşlama, büyük ölçekli üretim için mükemmeldir, şekillendirme kaliteli şekiller üretmek için güvenilirdir ve taşlama hassas uygulamalarda mükemmeldir. Üreticiler, her yöntemin avantajlarını ve dezavantajlarını dikkatlice değerlendirerek, kendi özel ihtiyaçları için en iyi yaklaşımı seçtiklerinden emin olabilirler.
YouTube kanalımız ekipman üretim süreci videolarımızla sık sık güncellenecektir, eğer ilgileniyorsanız, kanalımızı takip etmek için aşağıdaki bağlantıya tıklayabilirsiniz, her hafta harika videolar yayınlanıyor!
↓ ↓ ↓
Herhangi bir sorunuz varsa veya daha fazla yardıma ihtiyacınız varsa lütfen mühendisimizle iletişime geçmekten çekinmeyin: ben@pairgears.com .